18
Sep
Electrical submersible pump cable
Share:
I. Definition
Submerged oil pump cables are specialized cables used in oilfields for powering submerged oil pump units. They are typically installed in oil wells, connecting the lead cable at the bottom to the ground control cabinet at the top.
These cables come in two main types: round and flat. Flat cables are more common due to space limitations in oil well casings. However, their asymmetric structure can lead to hysteresis loss and heating due to an imbalanced magnetic field during power transmission.
Round cables are preferred when casing size allows. Their symmetric structure results in uniform electromagnetic field distribution, reducing interference and improving electromagnetic compatibility. Round cables are also easier to handle during installation and retrieval in oil wells.
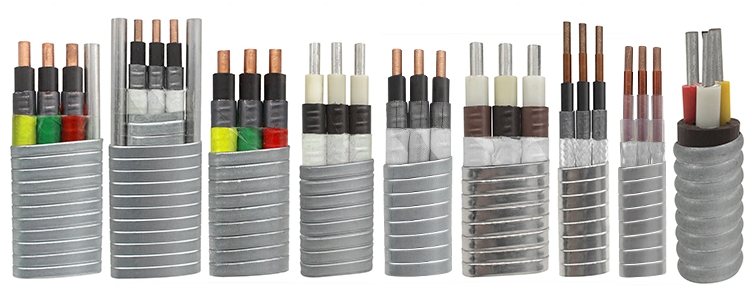
II. Structure
Submersible oil pump cables are critical for transmitting electrical energy to submerged pump units in harsh down hole environments characterized by high temperature, high pressure, and corrosive gases. To ensure long-term operation of the electric pump unit, these cables must possess superior electrical properties and resistance to extreme conditions.
Unlike standard power cables, submersible oil pump cables require specialized structural design and insulating materials to withstand the unique challenges of down hole operations. While maintaining excellent insulating properties, they are specifically engineered to endure the demanding conditions found in oil wells.
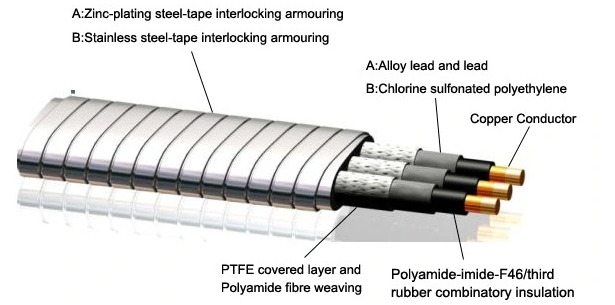
1. Conductor
The conductor in submersible oil pump cables is typically made from oxygen-free copper wire. To prevent accelerated aging of polypropylene insulation due to direct contact with copper, the conductor must be tin-plated when using polypropylene or modified polypropylene insulation.
For EPDM rubber insulation, a special bonding agent is applied to the conductor to prevent gas penetration between the conductor and insulation in down hole environments. This bonding agent, after vulcanization, ensures a tight seal between the conductor and the insulating layer.
These measures are crucial for maintaining the cable's integrity and performance in the challenging conditions of oil wells.
2. Insulation layer
(1) Polypropylene (PP) Insulation:
Thermoplastic, suitable for -20 to 100°C;
Brittle at low temperatures, prone to aging and deformation at high temperatures;
Extrusion temperature: 140-220°C.
(2)EPDM Insulation:
Thermosetting resin, widely used;
Operates in -40 to 180°C range;
Poor oil resistance; requires bonding agent and additional binding layer;
Extrusion temperature: 60-95°C.
(3)Polyimide/F46 Composite Film + EPDM Rubber Insulation:
Conductor coated with sintered polyimide/F46 composite film;
Special adhesive applied over film;
EPDM rubber extruded over adhesive;
Continuous vulcanization bonds composite film and EPDM rubber.
Each insulation type has specific properties and processing requirements, tailored for different operating conditions in submersible oil pump cables.
3.Shielding layer
Polytetrafluoroethylene (F40) film tape has good oil resistance, high temperature resistance, with F40 film tape wrapped around the insulation layer, blocking oil and gas on the ethylene propylene rubber invasion, to extend the service life of the cable.
4. Sheath layer
Cable Sheath Types:
1.Nitrile Rubber Sheath:
Good mechanical properties, oil and chemical resistance;
Surface fluted with splines to prevent damage during armoring and increase friction with chain steel belt;
Produced by extrusion, vulcanized at 170-190°C;
Extrusion temperature: 50-75°C.
2.Lead Sheath:
Made of pure lead or lead alloy;
Must be free of defects like sand holes, cracks, and impurities;
Produced by continuous lead extrusion at 290-390°C.
Both sheath types serve to protect the cable and provide specific properties suited for submersible oil pump applications. The nitrile rubber sheath offers better resistance to oil and chemicals, while the lead sheath provides a robust, impermeable layer.
5. Armoring layer
Chained steel belt armor plays a longitudinal force, while the sheath layer plays a key role in protection, if no armor protection, once the cable lifting up or sudden change in pressure, the sheath will dissolve and rupture. Steel belt armoring overlap winding, overlap rate > 35%, armoring the cable roundness control is more difficult, especially the lead sheath cable armoring is easy to lead layer deformation.
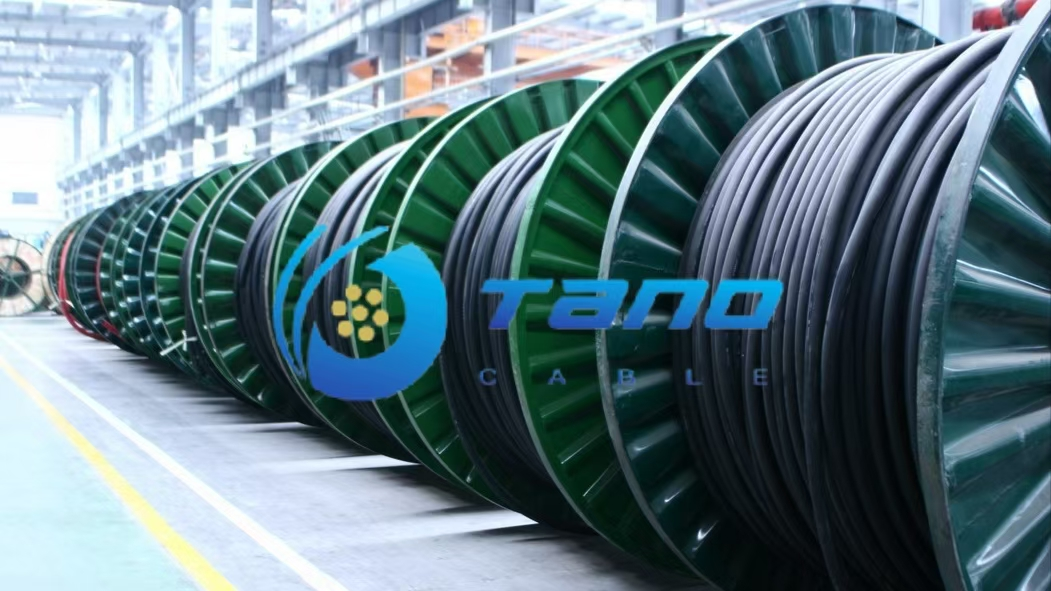
III. Consumption in practice
Submersible oil pump cable consumption is driven by four main factors:
1.New electric pump well installations in oilfields
2.Annual pump inspection cycles requiring cable updates
3.Cable repairs due to electrical breakdowns
4.Conversion of old oilfields from traditional pumping methods to electric submersible pump units for improved efficiency.
These cables are typically purchased in lengths exceeding 2800m per section, as joints are not permitted. Due to harsh operating conditions, they generally need replacement every 1 to 1.5 years.
The shift towards electric submersible pumps in aging oilfields with diminishing self-pumping capacity is a significant driver of cable demand, as these systems offer higher pumping efficiency compared to traditional methods like beam pumps.
If you have the need to purchase submersible oil pump cable, please feel free to consult TANO CABLE, we will provide you with reasonable and effective solutions to solve your problems and save your energy and money at the same time.
Submerged oil pump cables are specialized cables used in oilfields for powering submerged oil pump units. They are typically installed in oil wells, connecting the lead cable at the bottom to the ground control cabinet at the top.
These cables come in two main types: round and flat. Flat cables are more common due to space limitations in oil well casings. However, their asymmetric structure can lead to hysteresis loss and heating due to an imbalanced magnetic field during power transmission.
Round cables are preferred when casing size allows. Their symmetric structure results in uniform electromagnetic field distribution, reducing interference and improving electromagnetic compatibility. Round cables are also easier to handle during installation and retrieval in oil wells.
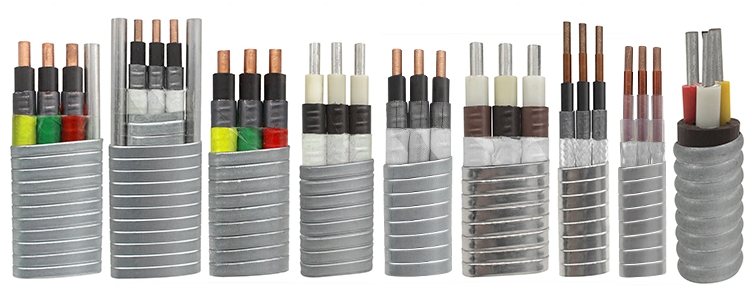
II. Structure
Submersible oil pump cables are critical for transmitting electrical energy to submerged pump units in harsh down hole environments characterized by high temperature, high pressure, and corrosive gases. To ensure long-term operation of the electric pump unit, these cables must possess superior electrical properties and resistance to extreme conditions.
Unlike standard power cables, submersible oil pump cables require specialized structural design and insulating materials to withstand the unique challenges of down hole operations. While maintaining excellent insulating properties, they are specifically engineered to endure the demanding conditions found in oil wells.
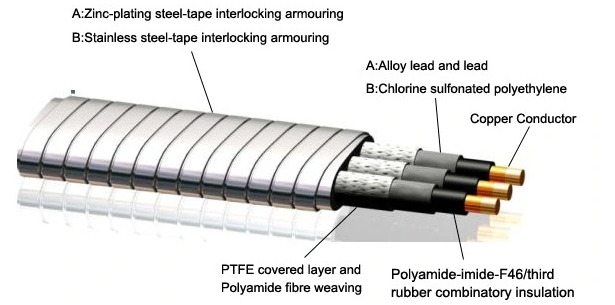
1. Conductor
The conductor in submersible oil pump cables is typically made from oxygen-free copper wire. To prevent accelerated aging of polypropylene insulation due to direct contact with copper, the conductor must be tin-plated when using polypropylene or modified polypropylene insulation.
For EPDM rubber insulation, a special bonding agent is applied to the conductor to prevent gas penetration between the conductor and insulation in down hole environments. This bonding agent, after vulcanization, ensures a tight seal between the conductor and the insulating layer.
These measures are crucial for maintaining the cable's integrity and performance in the challenging conditions of oil wells.
2. Insulation layer
(1) Polypropylene (PP) Insulation:
Thermoplastic, suitable for -20 to 100°C;
Brittle at low temperatures, prone to aging and deformation at high temperatures;
Extrusion temperature: 140-220°C.
(2)EPDM Insulation:
Thermosetting resin, widely used;
Operates in -40 to 180°C range;
Poor oil resistance; requires bonding agent and additional binding layer;
Extrusion temperature: 60-95°C.
(3)Polyimide/F46 Composite Film + EPDM Rubber Insulation:
Conductor coated with sintered polyimide/F46 composite film;
Special adhesive applied over film;
EPDM rubber extruded over adhesive;
Continuous vulcanization bonds composite film and EPDM rubber.
Each insulation type has specific properties and processing requirements, tailored for different operating conditions in submersible oil pump cables.
3.Shielding layer
Polytetrafluoroethylene (F40) film tape has good oil resistance, high temperature resistance, with F40 film tape wrapped around the insulation layer, blocking oil and gas on the ethylene propylene rubber invasion, to extend the service life of the cable.
4. Sheath layer
Cable Sheath Types:
1.Nitrile Rubber Sheath:
Good mechanical properties, oil and chemical resistance;
Surface fluted with splines to prevent damage during armoring and increase friction with chain steel belt;
Produced by extrusion, vulcanized at 170-190°C;
Extrusion temperature: 50-75°C.
2.Lead Sheath:
Made of pure lead or lead alloy;
Must be free of defects like sand holes, cracks, and impurities;
Produced by continuous lead extrusion at 290-390°C.
Both sheath types serve to protect the cable and provide specific properties suited for submersible oil pump applications. The nitrile rubber sheath offers better resistance to oil and chemicals, while the lead sheath provides a robust, impermeable layer.
5. Armoring layer
Chained steel belt armor plays a longitudinal force, while the sheath layer plays a key role in protection, if no armor protection, once the cable lifting up or sudden change in pressure, the sheath will dissolve and rupture. Steel belt armoring overlap winding, overlap rate > 35%, armoring the cable roundness control is more difficult, especially the lead sheath cable armoring is easy to lead layer deformation.
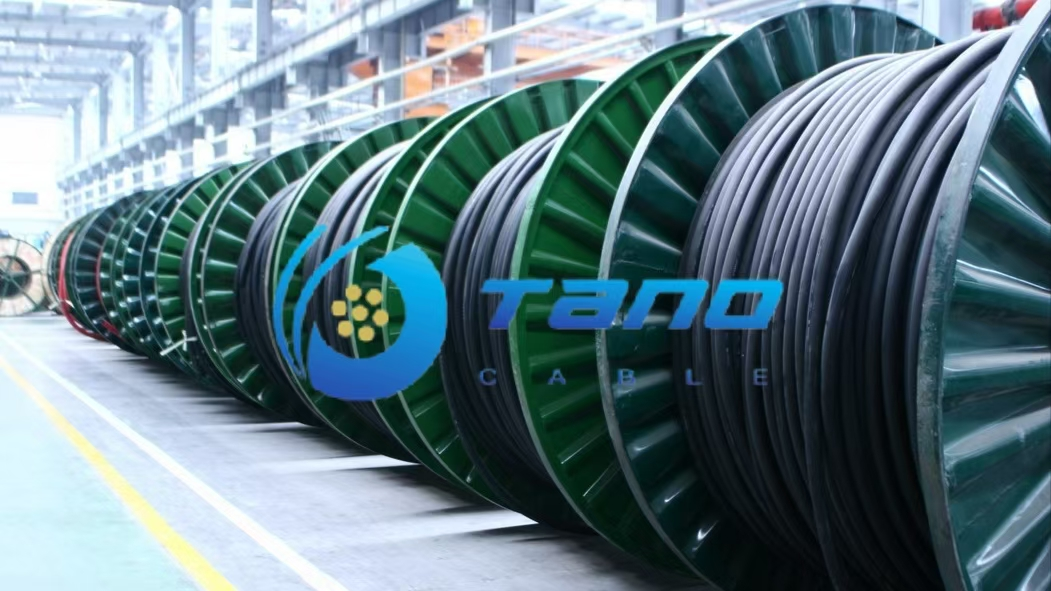
III. Consumption in practice
Submersible oil pump cable consumption is driven by four main factors:
1.New electric pump well installations in oilfields
2.Annual pump inspection cycles requiring cable updates
3.Cable repairs due to electrical breakdowns
4.Conversion of old oilfields from traditional pumping methods to electric submersible pump units for improved efficiency.
These cables are typically purchased in lengths exceeding 2800m per section, as joints are not permitted. Due to harsh operating conditions, they generally need replacement every 1 to 1.5 years.
The shift towards electric submersible pumps in aging oilfields with diminishing self-pumping capacity is a significant driver of cable demand, as these systems offer higher pumping efficiency compared to traditional methods like beam pumps.
If you have the need to purchase submersible oil pump cable, please feel free to consult TANO CABLE, we will provide you with reasonable and effective solutions to solve your problems and save your energy and money at the same time.
Next article: