12
Oct
The whole process control method of cable copper conductor anti-oxidation
Share:
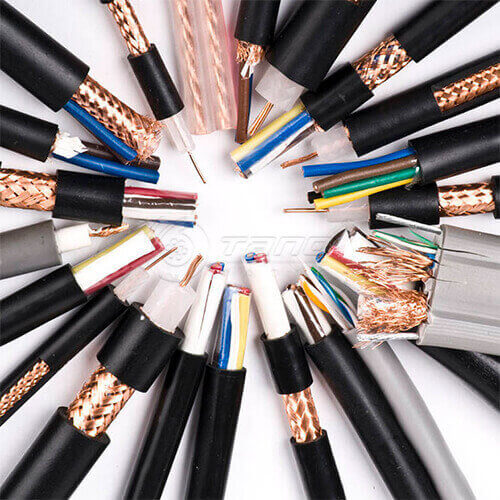
The atomic number of copper is 29, which belongs to transition metal, the density is 8.92g/cm3, the melting point is 1083.4℃, and it has good thermal and electrical conductivity. However, the surface of metal copper chemically reacts with oxygen in humid air to form Cu2(OH) 2CO3, or patina, usually shows that the surface of copper oxide is black in cable manufacturing plants. It is the existence of this phenomenon of surface oxidation of copper conductors that plagues many cable companies.
Below we take the production of medium voltage power cables as an example, from the arrival of copper rods to the production plant, storage, drawing, stranding, inner core storage to insulation extrusion, and analysis of effective control measures for each step.
Anti-oxidation control of copper conductor in the production process of medium voltage power cable
In principle, the metal copper for cables mainly includes physical methods to block copper from contact with humid air, cathodic protection redox method to prevent copper conductor oxidation, chemical methods to produce a passivation film on the copper conductor surface to prevent oxidation, or spray a special liquid on the surface of the conductor. protect. Take the production of medium voltage power cables as an example, the main method of anti-oxidation control in each process.
Transportation, testing and storage of copper rods before entering the factory
Most cable companies in my country use copper outsourcing, but most companies often ignore the control of the transportation process before the copper rod enters the factory. In the south of the Yangtze River and coastal areas (Jiangsu, Zhejiang, Fujian and Guangdong), the summer is long and rainy, and the copper rods are basically passed by heavy trucks. Transported to the company, through the author's understanding, many cable companies have not formulated the corresponding copper rod supplier transportation specifications, summer rainy packaging specifications and other systems, which makes it often appear that the copper rod surface is intact without oxidation and blackening when the copper rod supplier delivers the goods. When it reaches the cable enterprise user, the surface of the copper rod appears black, which brings unnecessary trouble.
The inspection of copper rods in the factory is basically in accordance with GB/T 3048.2 or the corporate standard of cable enterprises, with strict procedures. The storage of copper rods is generally placed in warehouses by cable companies. Generally, companies have stricter storage management methods. When copper rods are stored, especially in rainy summer, the copper rods must be covered with plastic sheeting or plastic film. Use the simplest The physical barrier method prevents the copper rod from contacting the humid air, which is often ignored by cable companies. When using copper rods in the workshop, it is necessary to visually check the copper rod rolls one by one for blackening, and control it from the source of production.
Control of copper rod drawing process
In this stage, the most commonly used 8mm copper rod for power cables is taken as an example. Nowadays, continuous annealing is generally used in wire drawing. It needs to go through the processes of pay-off, wire drawing and annealing, cooling, drying, and wire take-up. The mold of the corresponding specification is the first choice. Too small, if it is too small, it will force the crystal lattice of the metal copper to change and aggravate the sharp rise of the metal temperature.
Check the concentration of the emulsion before starting the machine to ensure that the concentration is qualified. During the pay-off process, the pay-off tension should be kept stable and uniform, and excessive vibration (vibration is unavoidable). The operator should pay close attention to the change of annealing temperature during the drawing process. After the wire is drawn, the conductor hardens, the elongation becomes smaller, and the DC resistivity of the conductor rises. There should be no residual emulsion on the surface of the copper conductor when the wire is drawn. Stored in a dry environment, waiting for circulation, but most cable companies omit the filming process because of the trouble of copper wire coating. The surface temperature of the conductor that has just been drawn into a loop is higher than room temperature, and there is a potential risk of oxidation in the rainy season.
The take-up place should ensure that the take-up reel is dry. After the take-up reel is filled, it should be sealed with a transparent plastic film. This is the same as the copper wire drawing. Many cable companies have also omitted this step. If this step causes the copper conductor to oxidize, it will be The impact of cables is still low, and for ultra-high voltage cables, the impact is unimaginable. After the copper conductor is drawn, stranded, and stored, the metal copper lattice shape is basically stable. Chemical cross-linking means that XLPE is uniformly extruded on the copper conductor under the conditions of cross-linking agent, antioxidant, coupling agent, etc. Before starting the pay-off reel filled with copper conductors, adjust the tension of the take-up and pay-off line to ensure the smooth operation of the equipment.
This Is cable knowledge from Henan Tano Cable Co.,Ltd. I hope it will be helpful to you.
Previous article:
Next article: